Breaking into Metalwork: Your No-Experience-Needed Roadmap to Seize America’s Industrial Shift
The clang of machinery and the hum of automation are rewriting the rules of metalwork careers. Forget outdated stereotypes of grimy workshops—today’s metal industry is a fusion of cutting-edge robotics, sustainable innovation, and untapped opportunities for newcomers. While traditional roles shrink (think: 73% of companies are automating repetitive tasks), a surge in roles like AI-integrated technicians and green manufacturing specialists is creating pathways for those willing to adapt. If you’re eyeing a career pivot or a fresh start, here’s how to capitalize on this seismic shift.
Why Metalwork Now? The Skills Gap That’s Your Golden Ticket
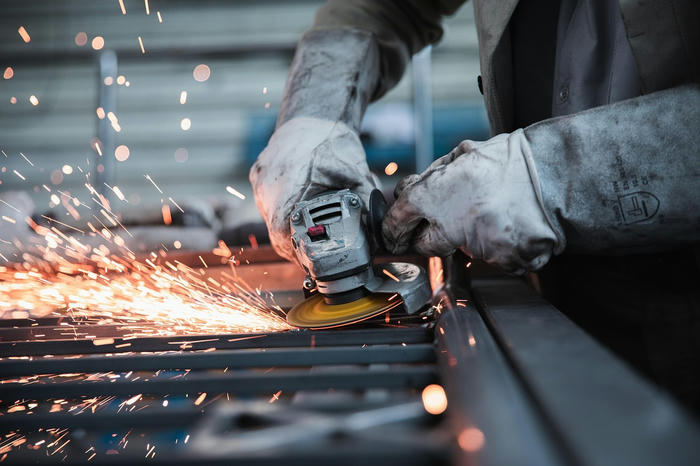
Automation isn’t stealing jobs—it’s reshaping them. The U.S. metal industry faces a critical shortage of 400,000 skilled workers by 2026, according to the National Association of Manufacturers. Employers aren’t just hiring; they’re hunting for problem-solvers who can bridge human ingenuity with machine precision. Take Ohio’s Titan Steelworks: they’ve eliminated 20% of manual welding roles but added 50 new positions in robotic maintenance and AI-driven quality control. These jobs start at $52,000 annually for novices who complete their 12-week upskilling program.
Action Step: Enroll in certifications like OSHA 10 or AWS Entry Welder. Platforms like Tooling U-SME offer low-cost courses tailored to automated systems.
The Rise of Hyper-Local Factories: Your Backyard Advantage
Global supply chain chaos has fueled a $30B reshoring wave, with states like Texas and Michigan leading the charge. Small-batch, localized production now dominates aerospace parts and EV component manufacturing. This isn’t just about patriotism—it’s practicality. A Detroit-based plant reduced lead times by 60% by sourcing materials within 200 miles. For workers, this means employers prioritize candidates who understand regional logistics and sustainability practices.
Case Study: Maria Gonzalez, a former retail manager in Phoenix, landed a $48K role as a production scheduler at a reshored aluminum plant after completing a 6-week Lean Manufacturing course. “They valued my customer service background for vendor negotiations,” she says.
Green Metalwork: Turn Climate Goals into Paychecks
The Inflation Reduction Act poured $6B into clean metal technologies, creating roles like carbon footprint analysts and recycling process engineers. Companies like Cleveland-Cliffs now require all new hires to complete sustainability modules, regardless of position. Entry-level “green techs” earn 18% more than traditional roles, reports the Steel Manufacturers Association.
Pro Tip: Master basics like ISO 14001 (environmental management) through educational webinars from the American Society of Mechanical Engineers. Add these credentials to your LinkedIn—recruiters filter for them.
From Zero to $65K: The Apprenticeship Revolution
Forget four-year degrees. Registered apprenticeships in states like Pennsylvania and Wisconsin combine paid on-the-job training with classroom learning, boasting 92% post-program employment rates. Mid-sized firms like Indiana’s Steelcraft Inc. now fast-track apprentices into roles like CNC programmers, with starting salaries exceeding $60K.
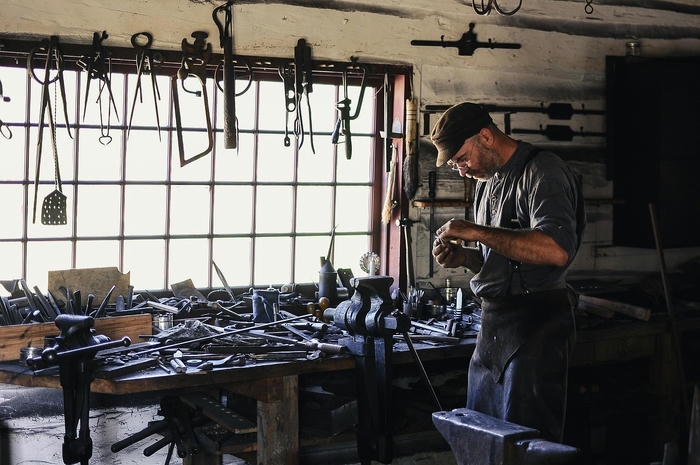
How to Start:
1.Visit Apprenticeship.gov to find programs near you.
2.Highlight transferable skills: Even retail or gig economy experience demonstrates adaptability—a top-rated skill per 70% of employers.
3.Network at local MFG Day events (October) where plants open doors to potential hires.
Future-Proofing Your Career: Skills That Outlast Robots
Automation handles tasks, but humans own strategy. The 2025 Future of Jobs Report ranks analytical thinking and creativity as the top survival skills. At Milwaukee’s ForgeTech, workers using AI design tools reduced material waste by 34%—a $2M annual saving. “Our best operators aren’t button-pushers; they’re innovators,” says CEO Lisa Tanaka.
Urgent Move: Join industry forums like Fabricators & Manufacturers Association International. Their virtual workshops on AI-assisted drafting or predictive maintenance cost under $100 and position you as a proactive candidate.
The Clock Is Ticking—Here’s Your Playbook
1.Utilize Local Resources: Libraries in industrial hubs (e.g., Pittsburgh, Grand Rapids) partner with local colleges for tool literacy workshops.
2.Target High-Growth States: Tennessee’s auto sector needs 1,200 new metalworkers monthly; Nevada’s battery plants are hiring 300+ monthly.
3.Negotiate Upfront: With 85% of firms prioritizing upskilling, ask employers about tuition reimbursement during interviews.
This isn’t just a job hunt—it’s a chance to redefine what’s possible in American manufacturing. The robots are here. The question is: Will you lead them or let them leave you behind? Sign up for a certification tonight. Your future self will thank you by payday.